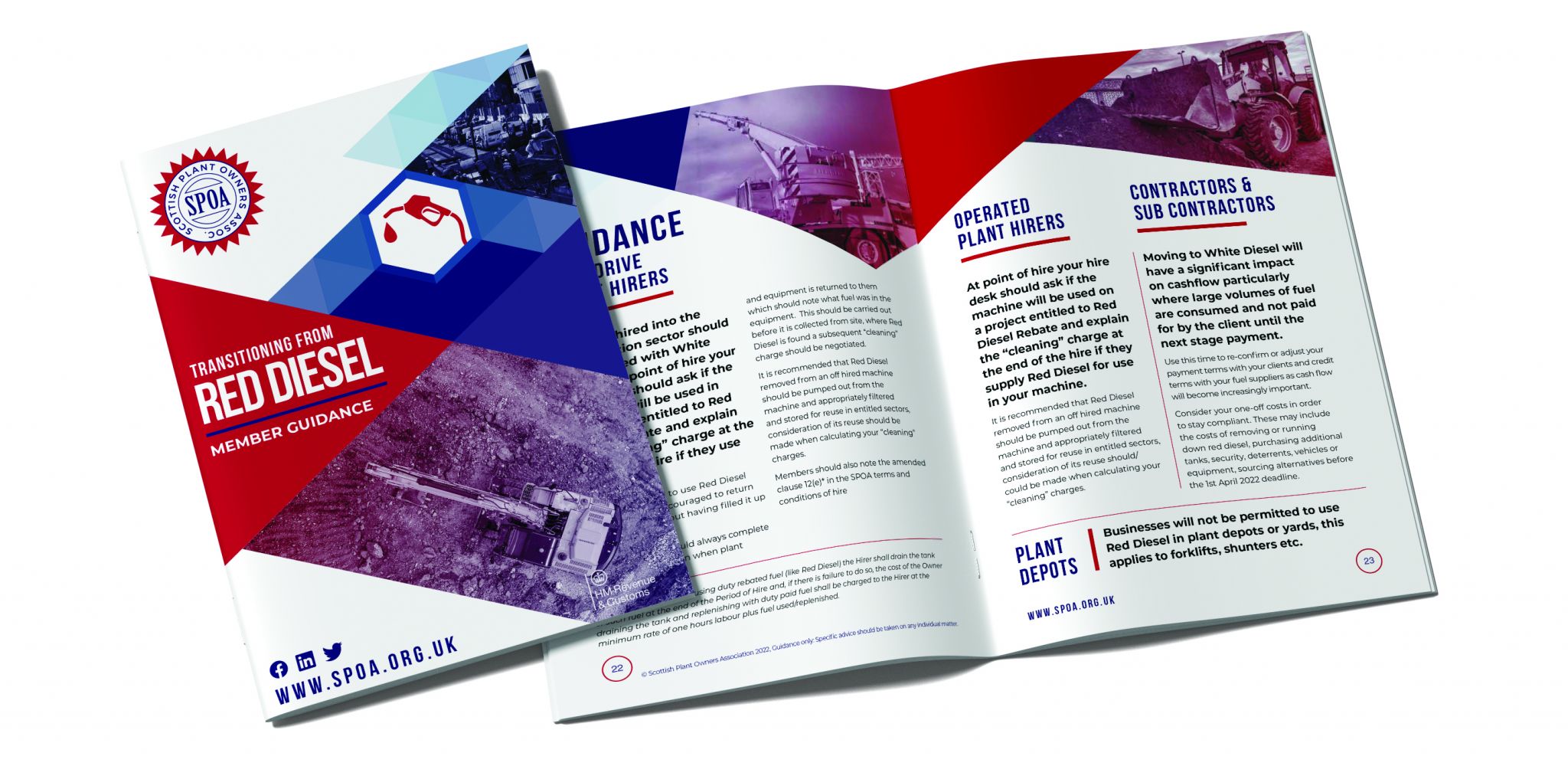
Sub Menu
It is more important than ever to prioritize and achieve long-term sustainable and verifiable reduction in energy consumption and carbon emissions.
There is no question that construction equipment is set to undergo radical changes over the next decade or so, as one of the major areas of emphasis going forward will be the continued drive towards electrification. Whilst diesel-electric hybrids and full electric-powered machines can provide lower total cost of ownership and deliver a positive impact on climate change in response to the industry’s decarbonisation challenge, there is still huge potential for improving the eco-friendliness of conventional engines, with the help of better fuels and lubricants.
It is also worth noting that diesel engine technology in non-road mobile machinery (eg articulated dumptrucks, excavators, wheel loaders, jaw crushers etc.) has progressed enormously in recent years, with construction equipment becoming more fuel-efficient and cleaner under EU Stage V emission standards.
Innovations in digitalisation and advanced data analytics are opening the door to improved efficiency, increased machinery uptime, safer working conditions and lower costs across the sector.
Yet one of the most effective measures that can bring substantial savings to a fleet is idle reduction. Switching the engine off during periods in the haul cycle for example reduces unnecessary machine operation and presents a cumulative fuel saving opportunity for heavy plant operators.
Digitalisation and plant automation have never been more important than in today’s climate, and the plant sector needs to seize this opportunity to provide greater transparency across the supply chain and help fleet owners make the best decisions possible in mobile asset management, with real-time intel into what is happening from the field. This includes machine hours and location, information on available equipment, and fleet idle time, fuel consumption and condition.’